Magnetic pumps are a go-to solution for industries dealing with hazardous, corrosive, or abrasive fluids. One of the most crucial factors that determine the pump’s performance, reliability, and longevity in these challenging environments is the materials used in its construction. To effectively transport aggressive liquids without risking damage or failure, the pump must be made from materials that are both corrosion-resistant and durable enough to withstand the abrasive nature of many industrial fluids. Let’s dive into what makes a magnetic pump suitable for these demanding applications.
First and foremost, the housing and wet-end components (those in direct contact with the fluid) must be crafted from high-grade corrosion-resistant materials. Stainless steel, particularly 316L and 904L, is commonly used due to its excellent resistance to corrosion and pitting, even in aggressive chemical environments. 316L stainless steel is particularly suited for applications in the chemical and pharmaceutical industries where resistance to chlorides and other corrosive agents is essential. For more extreme applications, such as those involving hydrochloric acid, sulfuric acid, or highly acidic materials, a pump made from high-alloy materials like Hastelloy C-276 or titanium can be indispensable. These materials offer superior resistance to corrosion, ensuring that even the most aggressive fluids won’t degrade the integrity of the pump over time.
Another key consideration is the material used for the magnetic coupling itself. Magnetic couplings in a pump eliminate the need for mechanical seals, which can be prone to wear and leakage. To maximize performance and reliability, the magnetic coupling should be made from highly durable materials such as rare-earth magnets, which offer strong magnetic forces while maintaining excellent resistance to heat and corrosion. When handling abrasive fluids, the non-metallic components, such as the bearings and isolators, should be made from advanced composite materials like carbon or ceramic. These materials not only resist corrosion but also provide low friction, helping to reduce wear in the system over time. The combination of rare-earth magnets with ceramic or carbon bearings ensures that the pump continues to operate efficiently and reliably under harsh conditions.
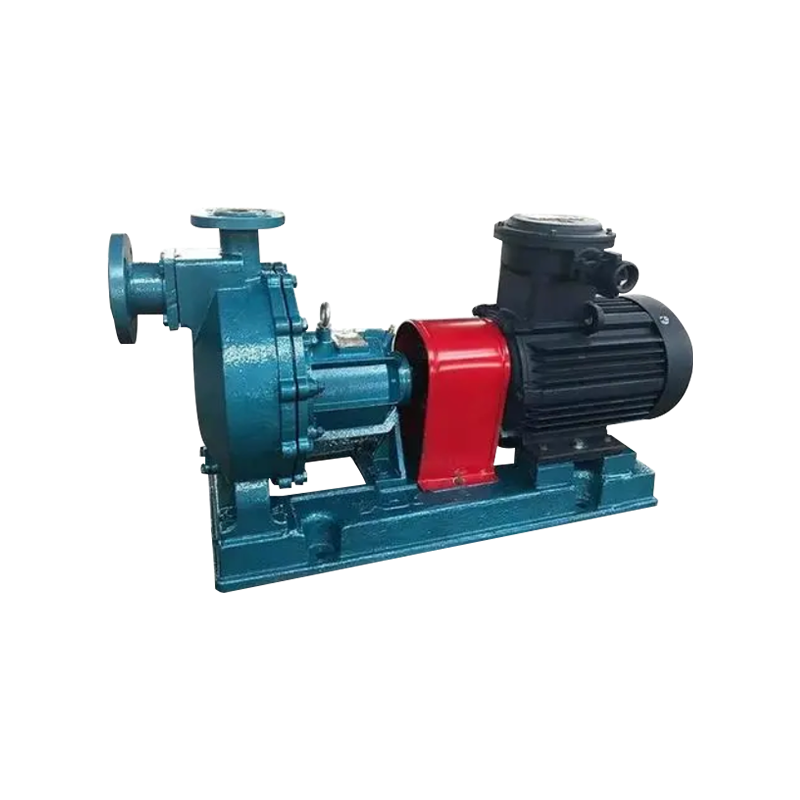
For the impeller and other critical moving parts, materials such as PVDF (Polyvinylidene Fluoride) or PFA (Perfluoroalkoxy) can be an excellent choice. These plastics are highly resistant to chemicals, UV degradation, and high temperatures, making them ideal for use in the most demanding fluid transfer applications. Additionally, they provide smooth surfaces that reduce the wear and tear associated with abrasive fluids, which helps the pump maintain its efficiency over long periods. In some cases, pumps may incorporate ceramic or carbide coatings to enhance their abrasion resistance. These coatings are designed to create a hard, smooth surface that minimizes the impact of solid particles or particulate-laden fluids, which can otherwise erode or damage the pump’s internals.
Choosing the right materials for a magnetic pump is not just about preventing corrosion; it's also about ensuring that the pump can withstand the physical stress caused by abrasive particles, fluctuating pressures, and extreme temperatures. A carefully selected material combination for the housing, impeller, magnetic coupling, and bearings will ensure that your magnetic pump operates reliably over a long lifespan, even when handling highly corrosive or abrasive fluids. Whether you're pumping acidic liquids in a chemical plant or transferring slurry in a mining operation, the right materials ensure the pump's efficiency, longevity, and safety.